The Hydro-Kinetic System
The cutting-edge Hydro-Kinetic wastewater treatment system utilizes advanced filtration technology to deliver the cleanest and most consistent effluent quality available. Specifically designed for homes and small businesses outside city sewer networks, the system combines extended aeration and attached growth processes with innovative nitrification-denitrification technology to treat wastewater effectively.
The Hydro-Kinetic system meets or exceeds stringent local regulations, especially in areas where nitrogen levels pose a threat to the environment. In coastal regions, nitrogen pollution can harm aquatic life, wildlife, and recreational areas. Our system reduces nitrogen levels to less than 10 mg/L, surpassing the USEPA standard for drinking water, showcasing its exceptional treatment capabilities.
During rigorous testing under NSF/ANSI Standards 40 and 245, the Hydro-Kinetic FEU system achieved:
- Certification as the only residential wastewater treatment system to pass two consecutive back-to-back tests without routine maintenance for 12 months.
- Exceptional results with effluent levels of 2.0 mg/L CBOD, 2.0 mg/L TSS, and 7.9 mg/L TN.
The system operates quietly and efficiently, automatically pre-treating, aerating, flow equalizing, and filtering wastewater, returning only the purest effluent to the environment, highlighting the system’s consistent, high-quality performance.
Routine Maintenance
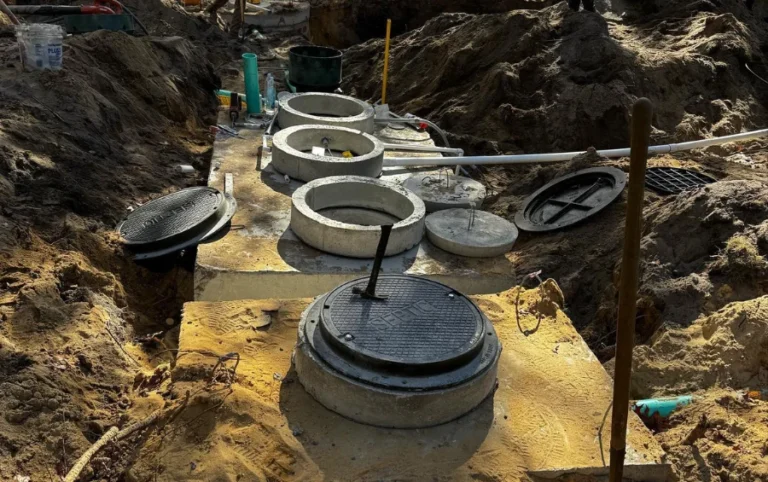
- See more
The following should be performed every 6 months by a qualified service technician through an approved service provider. (See Approved Service Providers List)
- If applicable, inspect the effluent discharge point to make sure there are no restrictions to the effluent flow. If restrictions are present, perform service as needed.
- If effluent sampling is required, it is recommended that a proper sampling port be installed downstream of the system.
- Inspect the vent cap, perimeter vent and air pump for objects, plants, insects or debris that could impede the air intake.Remove these items if present.
- Check the air pump for proper operation. Check the air filter and clean or replace as required. Check the aeration chamber for odor. A musty odor indicates the presence of aerobic conditions essential for proper treatment. A septic odor indicates inadequate aeration, suggesting that the delivery of air into the aeration chamber has been restricted.
- Check the aeration chamber and ensure the diffuser assembly is creating a rolling motion of the chamber contents. If a rolling motion is not visible, verify air pump operation. Remove and clean diffuser assembly if necessary.
- Check the anoxic chamber and ensure the mixing bar is operational. The recirculation pump operates on a pre-programmed on/off cycle, so press the reset button if necessary to verify operation.
- Inspect the flow equalization device. Rinse the design flow, sustained flow and peak flow ports with a garden hose and ensure they are free of debris. Clean the flow ports with a brush if necessary.
- Use the hopper scraping tool to gently scrape all surfaces of the clarification chamber hopper.
- Inspect the system to determine if complete pumping may be required. See "System Pumping" section of this document.
- Upon completion of the inspection, insure that all access covers are properly reinstalled. Any missing or damaged access covers should be immediately replaced.
DANGER: Make sure the system access covers are in good condition and securely installed on the mounting risers. Never allow access risers to be left uncovered or partially covered. Failure to secure access covers and safety nets could result in bodily injury, illness or death. Riser safety nets are available from Norweco for concrete or plastic risers. - Approved replacement parts are available from the authorized system dealer listed on the control center cover.
System Pumping
- The Hydro-Kinetic system is a biological treatment device and will not require pumping as often as a septic tank. Pumping of the system will likely be required at 3 to 5 year intervals depending upon system usage, loading and treatment requirements. If pumping is required more frequently than every 2 years, there is an operational problem with the system and it should be evaluated in greater detail.
- If the service technician suspects that the system may require pumping, a settleable solids test should be performed on a sample from the aeration chamber. The air pump must be removed from the aeration chamber riser to perform this test.
- Immediately after removing the air pump, dip a graduated cone or other clear container into the aeration chamber to a depth of 2 1⁄2 feet. Set the container on a level surface and then allow the solids to settle for 30 minutes while you complete the service inspection. Do not disturb the container during the test.
- After 30 minutes, read the level of solids and compare it with the total liquid volume in the container. Calculate the percentage of settled solids volume (i.e. 1⁄2 full of solids equals 50%). If the settled material contains large pockets of clear liquid, estimate the volume of these pockets and reduce the settled solids reading by that amount. A settled solids reading of up to 80% indicates no adjustments are necessary. A settled solids level greater than 80% in the aeration chamber indicates excessive solids and that the system should be pumped.
- If it is determined that pumping is required, contact a tank pumping service licensed by the local regulatory agency. The septage or biosolids from the system must be removed and disposed of in a manner consistent with federal, state and local regulations. Advise the pumping service that they will be pumping approximately 1,000 gallons.
- Turn off the air pump and recirculation pump before tank pumping.
- Remove the access cover from the aeration and clarification chambers. Unplug the air pump and disassemble the union located on the primary air connection. Remove the air pump, primary air connection and support base from the aeration riser. Use the universal tool to bend flexible diffuser tubing and remove the diffuser drop pipe assembly. Connect the suction hose to the pump being used to evacuate the chamber.
- Activate the pump and remove the aeration chamber contents. Pump the aeration chamber from the top down, to remove biologically inactive material. Feed the hose down as the liquid is being evacuated from the aeration chamber. It is not necessary to wash down the sidewalls or tank bottom. Pump only 75% of the volume out of the aeration chamber to facilitate plant re-start. Replace the diffuser drop pipe assembly. Reinstall the support base, primary air connection and air pump. Reassemble the union in the primary air connection and plug in the air pump. Replace both access covers.
- Next, pump the anoxic chamber. Remove the anoxic chamber access cover. Use the universal tool to bend flexible mixing bar tubing and remove the mixing bar drop pipe to allow access for the suction hose. Lower the hose until it contacts the bottom of the tank. Withdraw the hose approximately 2 inches. Completely pump 100% of the contents from the chamber. Reinstall the mixing bar drop pipe assembly and replace the access cover.
- The final chamber to pump is the pretreatment chamber. Remove the pretreatment chamber access cover. Break up the scum mat to facilitate pumping. Lower the hose until it contacts the bottom of the tank. Withdraw the hose approximately 2 inches. Activate the pump and remove 100% of the chamber contents. It is not necessary to wash down the sidewalls or tank bottom. If solids are so concentrated that the suction hose cannot withdraw them, tank contents may be backflushed to break up the solid matter. Replace the pretreatment chamber access cover.
- After pumping, refill all chambers to capacity with clean water. Return all plumbing and equipment to its properly installed location. Replace any access covers that were removed. DANGER: Make sure the system access covers are in good condition and securely installed on the mounting risers. Never allow access risers to be left uncovered or partially covered. Failure to secure access covers and safety nets could result in bodily injury, illness or death. Riser safety nets are available from Norweco for concrete or plastic risers. Turn on power to the air pump and the recirculation pump. Check for proper operation of all equipment.
Septic Odor from System
- No power to air pump: check air pump for proper operation. Insure the breaker is in the “on” position, the air pump is plugged in and power is present (check with test light from Tool Kaddy)
- Insufficient air delivery to aeration chamber: see “Control Center Alarming”
- Incomplete treatment due to hydraulic overloading: see “Hydraulic Overloading of System”
- Water softener backwash discharging into system: notify owner to remove backwash line from system
- Excessive solids in aeration chamber: evaluate chamber and pump if necessary
- Excessive solids in anoxic chamber: evaluate chamber and pump if necessary.